Tesla
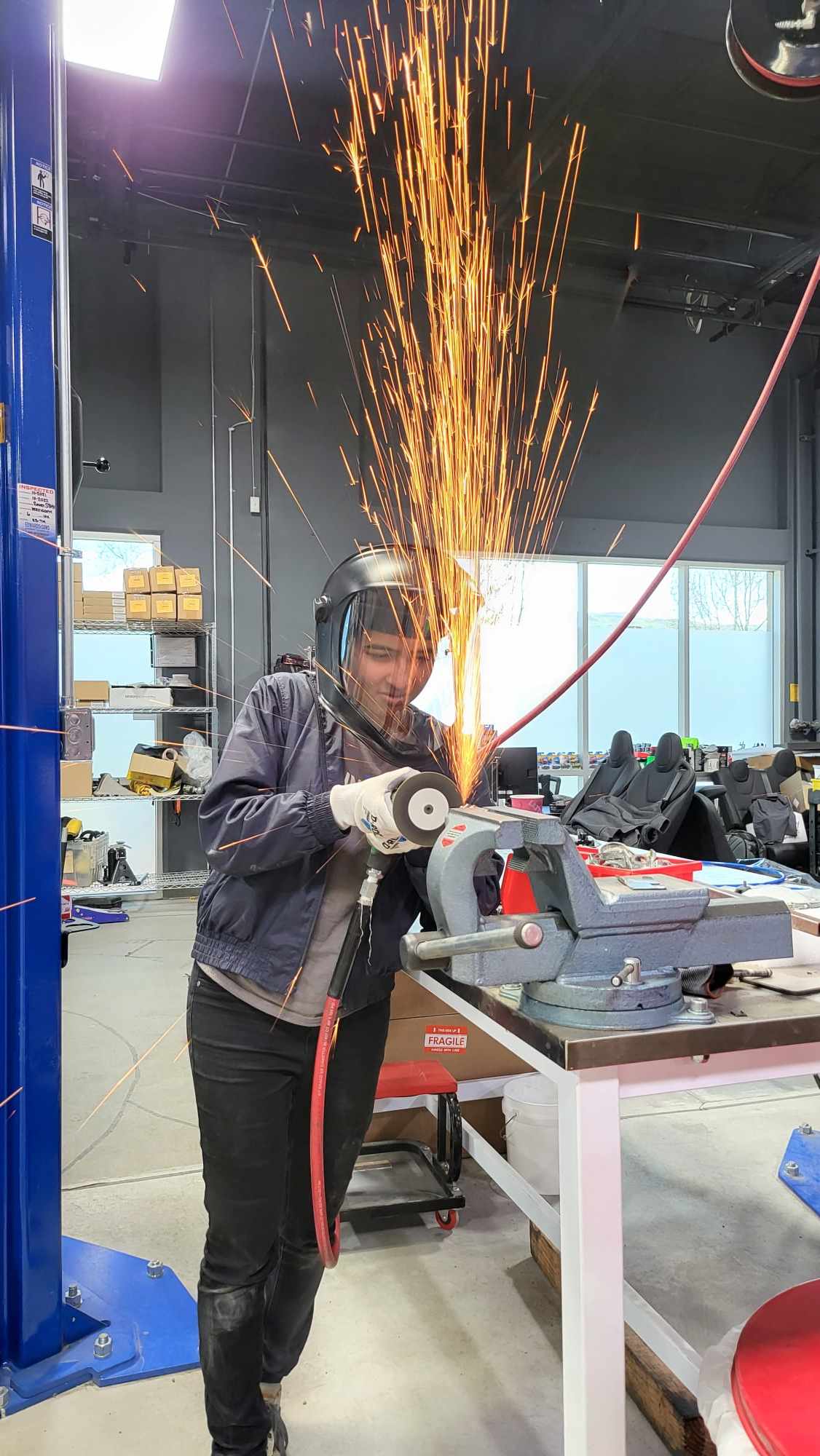
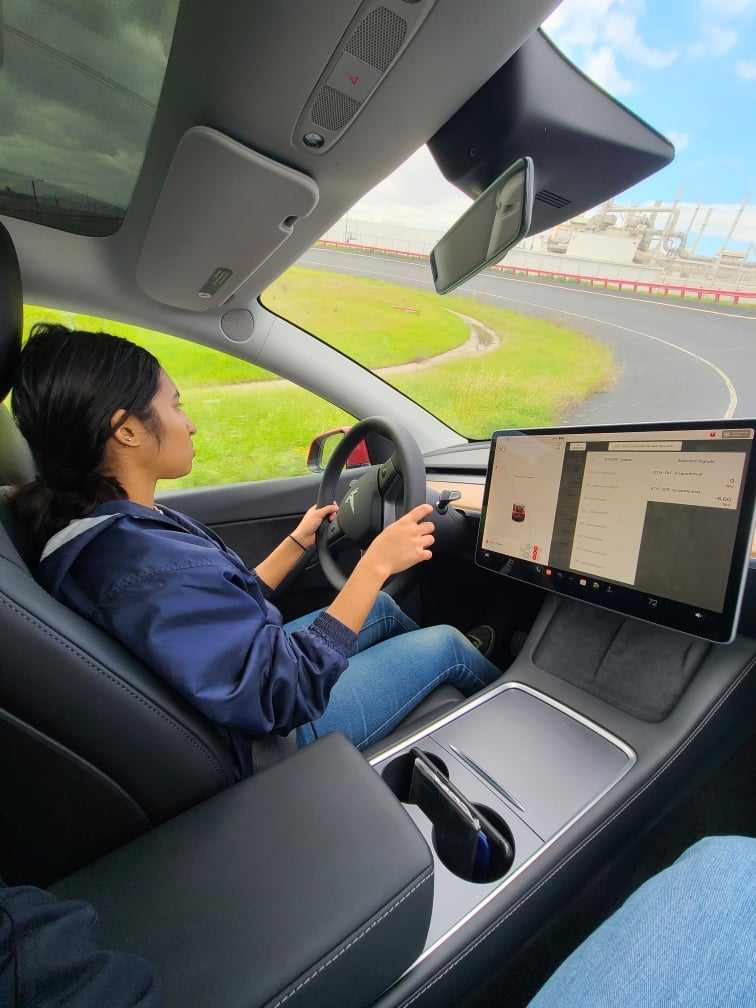
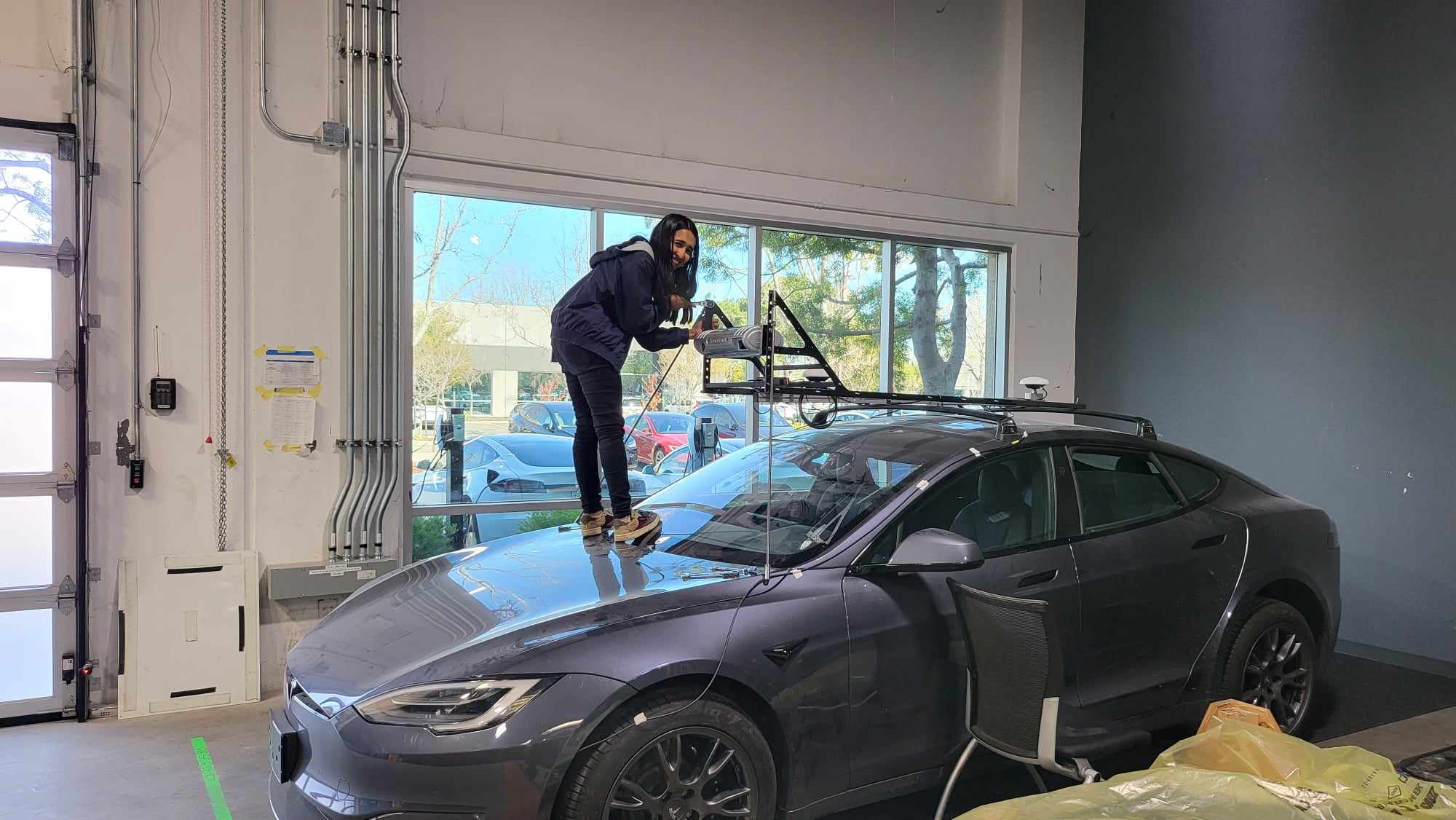
While at Tesla, I worked on a few different projects in addition to being responsible for multiple vehicle-level tests:
powertrain, durability, and suspension strength. I worked on creating a pothole detection algorithm in MATLAB, created a pitch compensation algorithm,
and wrote data parsing scripts in Python.
My internship projects included creating a pothole detection algorithm and determining road roughness. To create a pothole detection algorithm, I found multiple
local potholes at various sizes and depths and tested hitting them at various speeds. I then created variable thresholds for wheel speed, vehicle speed, longitudinal
acceleration, and brake torque. I determined these thresholds through the data I obtained and wrote a MATLAB script to iterate through CAN data and find potholes determined
by the thresholds I set. This algorithm is able to detect approximately 96% of the potholes that I hit (125/130). These thresholds will be implemented by the firmware team
for pothole data collection on large fleets of our vehicles.
To determine road roughness, I worked with both a commercial LIDAR scanning sensor as well as laser sensors. I mounted a laser sensor in front of each wheel
on a Model S, on which the commercial road scanning device is also mounted. By driving through various roads, I was able to look at the road roughness data of the
road in front of each wheel. The laser sensor raw output is a voltage representing the distance between the laser sensor and the road. I created a calibration curve
to convert from voltage to distance, and I implemented pitch compensation by integrating the pitch rate signal from the vehicle and using trigonometry to ensure the
pitch of the vehicle does not affect the height measurement from the laser sensors. I was able to successfully measure the roughness of the road via both the commercial
road scanning device as well as the laser sensors, which means that we will be able to measure road roughness on many more vehicles using the laser sensors, and will
not have to depend on an off-the-shelf product.
Regarding vehicle-level tests, my responsibilities included working with operators and technicians to ensure vehicles were properly prepped and returned,
implementing the various testing procedures with operators, working with the logistics team for vehicle delivery and proving ground usage, CAN signal
analysis, and real-time problem solving for any issues that came up. For example, during a durability test that I was running, we had an issue with
the camera harness on the vehicle. This issue was discovered as we ran a self-test on the vehicle every day, and I created a data parsing script in
Python to tell us whether the harness was functioning. After we saw the failure, I connected with the camera team, discussed next steps, and sent the
faulty harness to them, replacing it with a new harness we received.